In today's manufacturing landscape, the utilization of 3D printing powder has surged, revolutionizing industries from aerospace to healthcare. As the demand for 3D-printed products escalates, so does the necessity for efficient and precise powder screening processes.
When it comes to sieving 3D printing powder, a closed system is essential. These powders are often sensitive to environmental factors like humidity and contamination. To ensure optimal quality, an enclosed screening process is crucial.
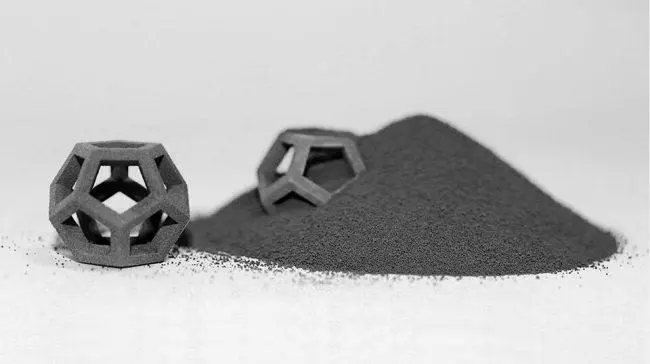
Our custom-designed rotary vibrating screen addresses these challenges effectively. Let’s explore its key features:
1. Sealed Design: The rotary vibrating screens ensure ensures containment of the powder, preventing spillage, minimizing dust emissions and reduce the material waste. This feature not only maintains a clean working environment but also enhances workplace safety.
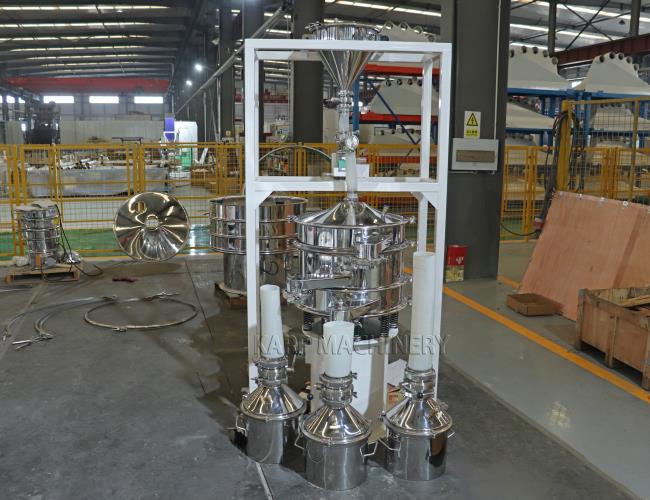
2. Ultrasonic Cleaning Devices: Mesh blockage can disrupt the screening process. To combat this, our screens are equipped with ultrasonic cleaning devices. These devices prevent clogging, ensuring continuous and efficient screening operations. Increased productivity.
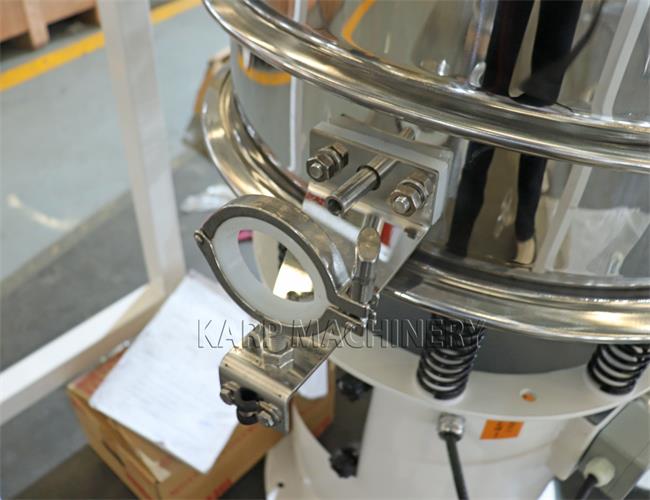
3. Quick-Flange Connection: Need to access the powder? No problem. Our rotary vibrating screens feature a quick-flange connection, allowing easy material retrieval and maintenance. Whether it’s for routine upkeep or sample collection, this user-friendly design streamlines the process.
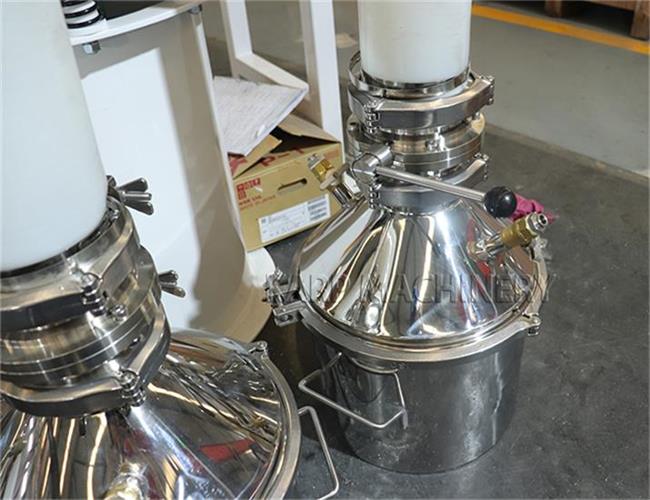
At Karp Machinery, we specialize in delivering leading solutions tailored to our clients' needs. By choosing Karp Machinery, you gain access to customized solutions and leading screening technology, empowering your business to thrive in the worldwide competitive manufacturing landscape.