Tumbler screen and rotary vibrating screens are both popular types of industrial screening equipment, but they have distinct differences in the following aspects.
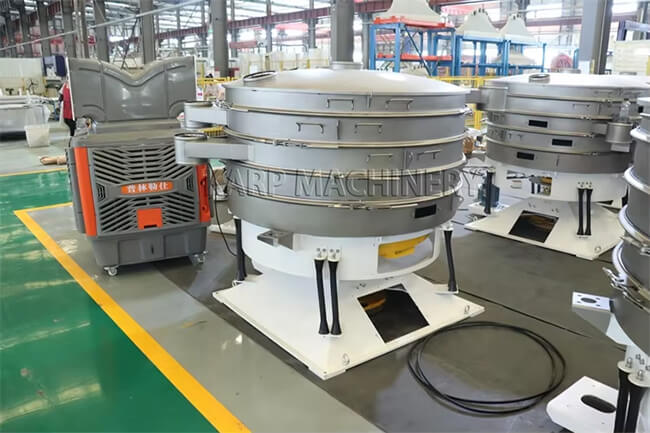
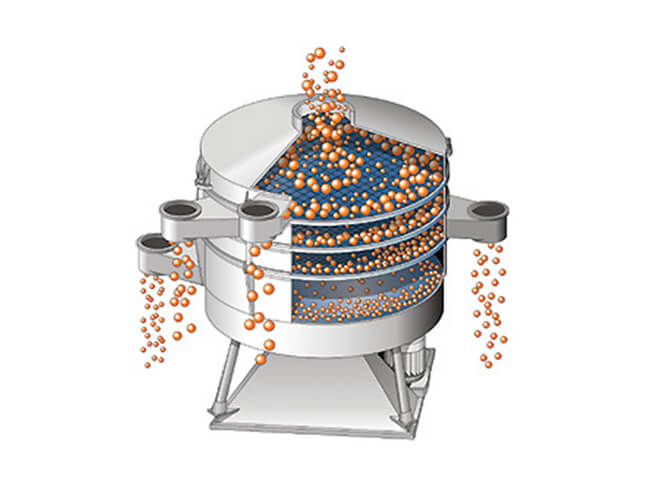
- Capacity:
The maximum size of tumbler screens is 2600mm in diameter, with a single effective sieving area of 5.3m². While the maximum diameter of rotary vibrating screen is 1500mm, the effective sieving area in single layer is 1.5m². So under the same screening conditions, the capacity of tumbler screens is much greater than rotary vibrating screen.
Then why can't the rotary vibrating screens be made of large diameter? The main reason is the frequency. The tumbler screen uses an ordinary motor, the screen speed is about 220 RPM, the low-frequency swing, and gentle movement. The rotary vibration screen uses a vibration motor, the speed is about 1500 RPM, the frequency is high, and the rotary vibration screen with a diameter greater than 1500mm may have risks such as cracking.
- Layer:
The swing screen can be up to 5 decks, which can achieve the classification of 6 sections at one time. The rotary vibration screen is recommended not to exceed 4 layers, the reason is: the swinging screen is driven by the drive shaft, the swing amplitude is consistent, the movement of each layer of material is consistent, the number of layers will not affect its screening effect. Rotary vibrating screen is to screen materials by high-speed vibration, the more layers there are, the less exciting force there is at the top layer, so affecting the upper layer screening. So it not recommended that the screen layer is too much.
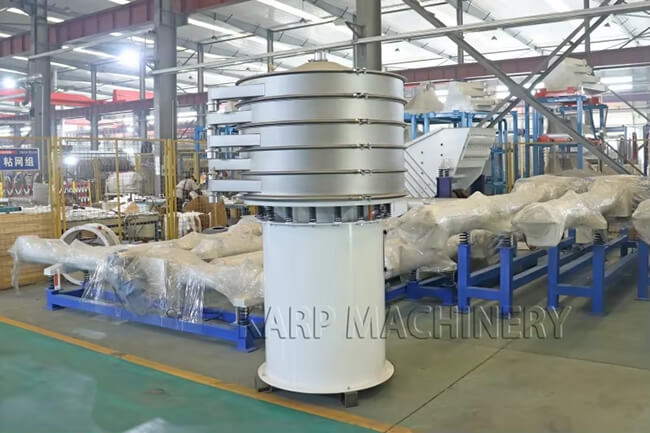
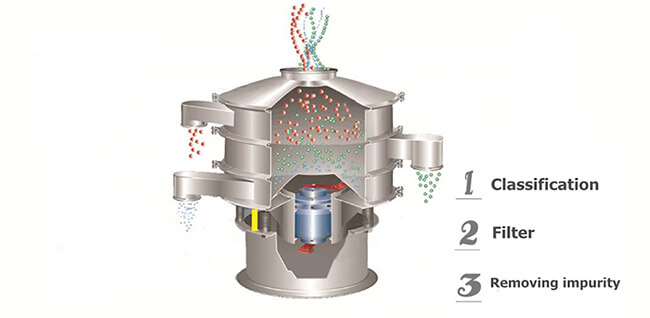
- Effect on raw materials:
The working of tumbler screen is a slight swinging movement, and there is no high-speed vibration. So the impact on the material is very small, and it will not destroy the shape of the material, and greatly improve the yield of the material. The rotary vibrating screen is to screen the material through high-speed vibration, there is slight secondary crushing of the material. So the rotary vibrating screen is not suitable for sieving granular crystalline materials, such as chicken essence, MSG, sugar, etc.